PET sheet extrusion line |
We developed a new extrusion line for the production of three-layer thermoforming sheets from virgin and regrind poly(ethylene terephthalate) (PET) material that eliminates the need of pre-drying. The new line includes two corotating twin-screw extruders that are equipped with special degassing units. The first twin-screw extruder allows the production of the core layer from regrind PET materials while the second one produces the two outer layers from virgin PET materials. The resulting sheets are highly transparent and can be subsequently thermoformed to produce packaging such as blisters. Moreover such a thermoforming sheet line offers important raw material cost saving as well as lower energy consumption compared with conventional systems.
In recent years the demand for using PET bottle waste to produce also thermoformed sheet has been growing steadily. Several technologies were applied, all of them trying to avoid drying of flakes (with relative high costs) before being fed to the extruder. In order to keep manufacturing costs down, we use a twin screw extruder with vacuum degassing.
The sheet thus obtained guarantees high quality, with a minimum loss of I.V. measured in the extruded sheet in relation to initial waste values. It is well known how strongly moisture influences the intrinsic viscosity of the PET product to be later thermoformed.
Such moisture can be thoroughly eliminated by means of a very efficient vacuum system equipped with a high performance special pump. The use of the sheet for food packaging requires that only virgin material may be in contact with foodstuffs.
Therefore the central extruder, fed with flakes, is complemented by a co-extruder to be fed with virgin material. This allows the production of a multi-foil sheet A-B-A in a 5-90-5% ratio, respectively. |
|
|
|
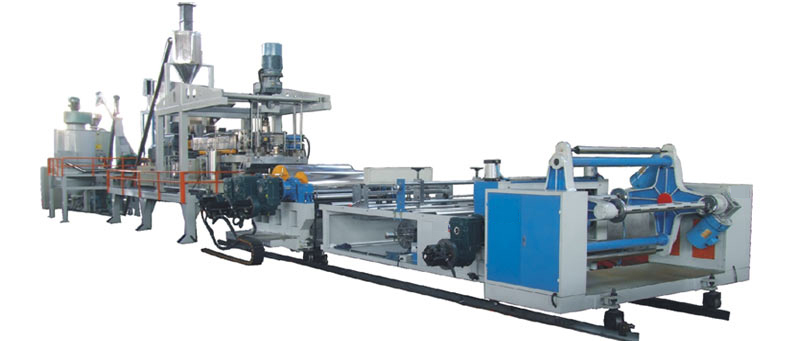 |